Investing in facility maintenance: a key to long-term success for life sciences organizations
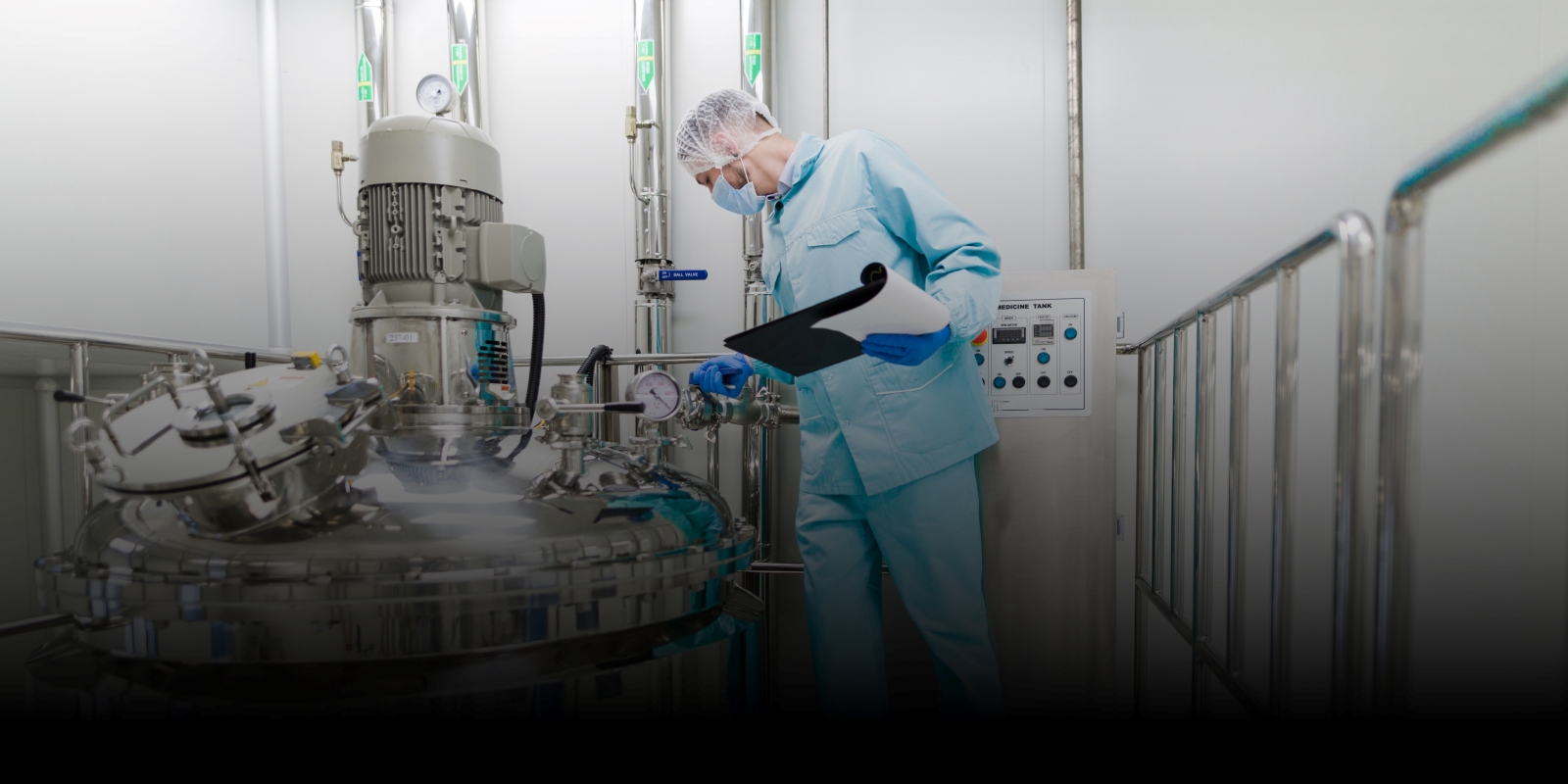
Maintaining a facility in the life sciences industry requires an understanding of various aspects including regulatory requirements, product quality standards, auditing processes, corrosion prevention methods, and cost optimization techniques. Our Unispace Life Sciences Global Benchmark Report Forefront provides key insights into the maintenance programs of organizations in the life sciences industry. In this report we surveyed 180 global industry leaders, interviewed 12 blue-chip pharma companies, and featured insights from our roundtable hosted by The International Society for Pharmaceutical Engineering (ISPE) on topics unique to pharmaceutical engineering teams.
Maintenance standards and accountability
According to the survey results, almost 54% of respondents do not have a standard for facility maintenance. Only 19% of organizations have a maintenance program specifically for facility finish while 29% have implemented facility finish upgrades on an annual basis. Most of these organizations depend on individual sites to complete their own audits, with just 16% of respondents completing global view audits to ensure their facilities meet standards.
When it comes to budgeting for maintenance activities, 35% of respondents don’t know how much they’re investing in maintenance overall. It's clear from this data that many organizations need to review their budgets and invest more in facility maintenance if they want to remain competitive within the market. 44% of respondents reported spending between 1-10% of their budget on facility maintenance, with 32% spending 1-5 % of CAPEX specifically on elegance per year.
Facility maintenance is critical to talent attraction
Best practices for facility maintenance need to be treated as critical to the long-term success of a pharmaceutical engineering workplace. The vast majority (80%) of respondents invested in non-production areas with a view to attracting and retaining talent. A lack of resources and experienced talent has impeded complex innovation and capital projects across all sectors; upgrading and investing more in facilities has become necessary as companies compete for talent within the sector. In terms of measuring the success of facility regulation, 71% of respondents base maintenance quality standards on meeting or exceeding baseline regulatory requirements, while 45% of quality standards are driven by site audits or work orders.
Managing rouge corrosion
Another challenge facing maintenance is the management of rouge corrosion, which is a natural occurrence for water and heat processes within stainless steel vessels and piping. Our research showed that 70% of those surveyed have programs in place specifically to manage rouge, and that most of these programs are driven by maintenance leaders. Over the next five years, however, 34% of respondents will choose to implement identical standards across all systems. Using the OODA loop (Observe, Orient, Decide, Act) to monitor, selecting MOC resistant to oxidation/chlorination, and using mild acids like OPA/nitric acid as part of the Clean-in-Place (CIP) cycles are effective ways to manage rouge corrosion. It's important that organizations develop rigorous procedures with clear action plans when dealing with rouge corrosion so they can mitigate any risks associated with it quickly and effectively.
Procedural best practices include online/inline rouge monitors, development of playbook and cross network standards for monitoring/acting and using visual aids and criteria to determine rouge levels and subsequent appropriate action.
Facility management is critical to delivering on expectations
In conclusion, effective facility management plays an integral role in ensuring successful operations within the life sciences industry, given its complex nature and criticality of products produced. With best practices in place, organizations will be able to maintain compliant surfaces and clean working environments that attract and retain talent all while optimizing costs to deliver high-quality end products that meet expectations of customers and stakeholders alike.