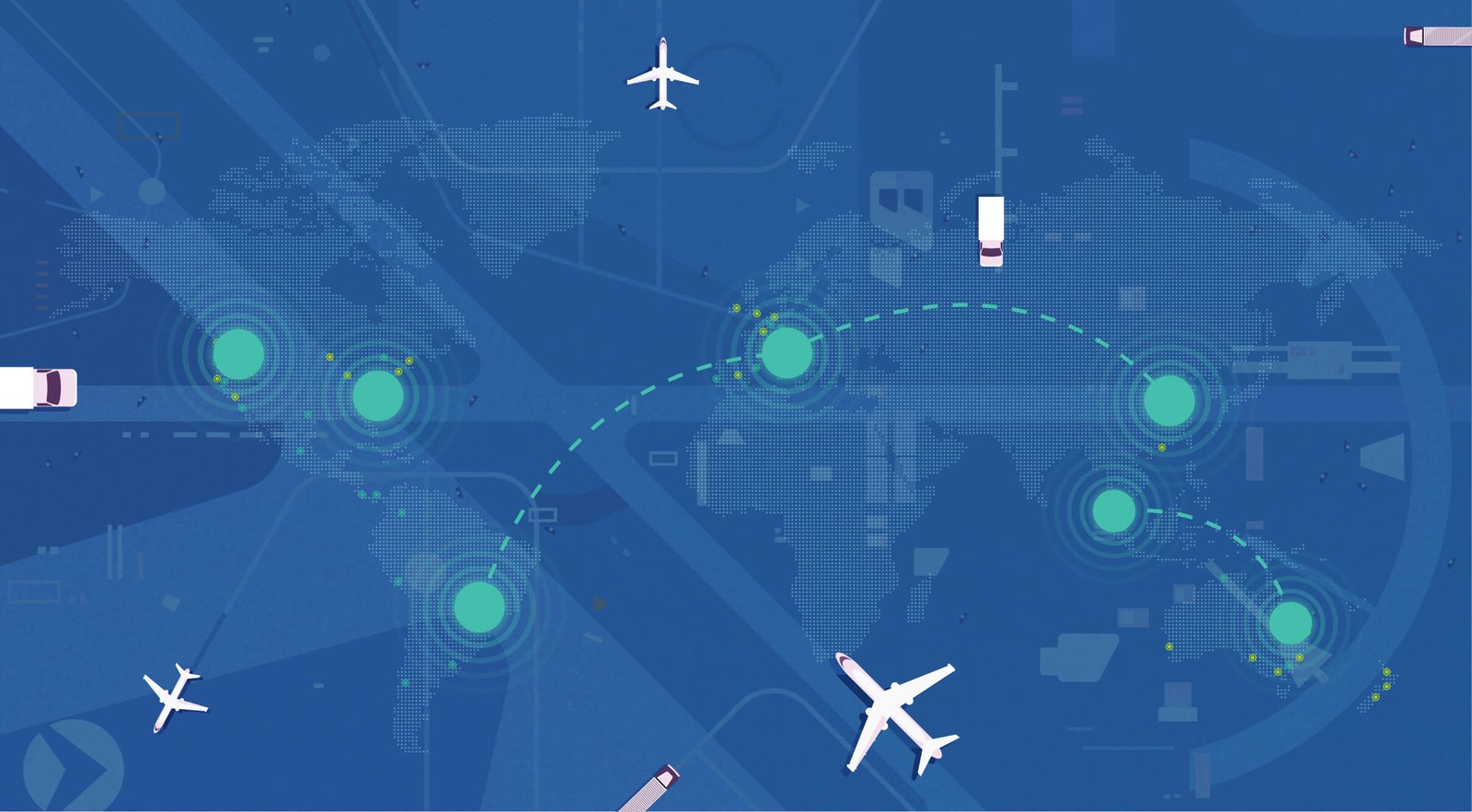
With COVID-19 a growing concern for businesses across the world, we take a look at the common questions around its impact on current and upcoming workplace projects, and the proactive measures we’re putting in place to minimise disruption.
Since news first emerged about the spread of COVID-19, there’s been growing concern about the inevitable disruption to supply chains and the knock-on impact for project delivery. With WHO declaring a global pandemic status, these concerns have naturally increased since.
Our ongoing conversations with clients all over the world align with this and reveal understandable concerns about the likely impact COVID-19 will have on their current workplace plans – both those currently being delivered as well as those in the pre-construction strategy and design phase.
As Ryan Caffyn-Parsons, Global Director, Delivery at Unispace explains, “The last thing clients want during this period is the prospect of a planned workplace move being delayed or cancelled, or carrying a far greater cost than originally budgeted for.”
Understanding the risk profile of your supply chain
“Unispace’s global presence gives us a wealth of insight into what’s happening across the supply chain. We speak to hundreds of local partners every day, and we operate without silos internally, meaning that we can quickly share new, on-the-ground updates from one market with our entire network,” said Ryan.
In every region, we’re speaking with as many suppliers, contractors and engineers as possible each day, to give us a complete picture of the wider market. This is crucial given that the COVID-19 outbreak impacts not only suppliers of furniture and fittings, but also of components used by other local manufacturers and assembly houses all over the world. We are continuing to monitor the situation closely, as well as encouraging our own suppliers and contractors to think holistically about their own supply chains and better anticipate future challenges.
Immediate labour implications
Many local construction workforces are comprised of overseas workers employed on temporary or permanent work permits. We’ve already seen some of those workers repatriated, while others have found themselves unable to return to work following trips back to their home country.
As COVID-19 has spread globally, many countries have imposed quarantine measures, travel bans, and social distancing rules while others have preferred a ‘wait and see’ approach – all of which has made it harder for contractors to effectively manage their local workforces and ensure there are sufficient numbers on site at any given time.
In addition to ongoing construction and fit-out work, we’ve heard from many clients that are being forced to manage projects remotely due to mandatory home-working policies. As a business of more than 700 people, active in almost 50 locations across 25 countries, we’re in the same position as many of our clients when it comes to ensuring business continuity while protecting our staff – and the communities they belong to.
Identifying issues before they escalate
We’ve set up a dedicated internal information-sharing resource for alerting teams to potential supply chain issues, wherever and whenever they occur. The result is that we’re able to identify potential cost increases early, for example where we have seen levies put on furniture items due to perceived stock shortages, and quickly find alternative supplier options using the Unispace national and international network.
Unispace’s standard practice is to source local materials wherever possible to minimise the carbon footprint of our projects, mitigate risk by avoiding reliance on overseas products with long lead times and support the local economy. It’s therefore important that regular communication with local suppliers helps us ensure they’re not experiencing challenges of their own as, “We need as much insight as possible to make effective judgement calls on suppliers,” says Simon Pearson, Regional Principal, Delivery – EMEA at Unispace. “It may be that we have to switch if the impact is set to be long-term, but we also need to be mindful of groupthink. If too many firms switch, there’s a risk of overloading local suppliers and simply moving the shortage from one location to another.”
Delivering work on-the-ground
Our business is set up to minimise the reliance on travel to service our projects. “One of our global clients was considering putting all of their projects on hold,” says Simon Raper, Global Principal, Unispace. “As a result of our footprint, cloud-based design tools and delivery technologies, we were able to offer an online alternative to face-to-face meetings on projects, and give them the confidence that we can keep things moving for them.” Our local presence and close relationships with in-market contractors means that we often serve as our clients’ eyes and ears across territories in which they’re not yet active. Right now, we’re in constant contact with clients’ real estate teams, as well as using our Procore project management software to give real-time insights into the status of ongoing projects.
For pre-construction projects, our teams can work remotely in the event of country-specific travel bans, lock downs or quarantine measures. Because we use locally based partners, we’re not currently anticipating any significant impact on our ability to deliver ongoing fit-outs. Again, by monitoring local health guidance in real-time, we’re able to take swift action in markets where the business impact of COVID-19 is escalating at speed.
“Our first priority is cutting through the noise and educating contractors on the reality of the situation,” says Kevin McCabe, Unispace Regional Principal, Delivery – APAC. “We’ve issued our teams and contractors with appropriate guidance on spotting the symptoms and preventing the spread of COVID-19. We’ve also requested details from each firm of any employee who has been travelling or quarantined, again allowing us to safeguard both the people on site and clients visiting.”
What will be the ultimate impact of COVID-19?
It’s difficult to predict the longer-term financial consequences of COVID-19 for the world’s economies, but what does seem clear is that the outbreak will have a longer-term impact on how global business is transacted, how businesses organise and structure their workforces and supply chains, and on more general risk preparedness and mitigation strategies.
“We’ve always designed our projects to have both a Plan A and Plan B in place, should the unforeseen occur,” explains Kevin. “One of the consequences of COVID-19 is that we’re now building in a Plan C and D as well, so that we can continue to keep projects on-track, even in the most extreme of operating conditions.”
In the coming weeks we’ll be publishing further content analysing the long-term consequences of COVID-19 upon the business world and the workplace lessons we can learn from the outbreak.
In the meantime, if you’re considering a new workplace project and have concerns about the potential impact of COVID-19 on your plans, please get in touch with our team and we’ll be happy to give you an objective view on the best way to proceed.